Abstract
Monitoring of bolt looseness is essential for ensuring the safety and reliability of equipment and structures with bolted connections. It is well known that tangential damping has an important influence on energy dissipation during wave propagation across the bolted joints, which require different levels of preload. In this paper, the energy dissipation generated by tangential damping of the bolted joints under different bolt preloads was modeled analytically based on fractal contact theory, which took the imperfect interface into account. A saturation value exists with the increase of the bolt preload, and the center frequency of emitted signal is demonstrated to affect the received energy significantly. Compared with previous similar studies based on experimental techniques and numerical method, the investigation presented in this paper explains the phenomenon from the inherent mechanism, and achieves the accurate quantitative monitoring of bolt looseness directly, rather than an indirect failure index. Finally, the validity of the proposed method in this paper was demonstrated with an experimental study of a bolted joint with different preload levels.
Export citation and abstract BibTeX RIS
1. Introduction
The bolt loosening caused by insufficient preload can result in disastrous consequences, therefore monitoring the pre-load on bolted joints is essential to ensure the safety and reliability of structures that use bolted connection. A common way to detect loss of preload or bolt looseness is the use of installed load cell or the strain gauge. However, they are not practical in many instances. Vibration-based techniques [1, 2] have been applied to monitoring of bolt loosening based on detecting the change of dynamic characteristics, such as frequency response function [3] or mode shapes [4] of the fastening parts. A general review of monitoring of a bolted connection is given in [5].
Piezoceramic materials, which have attractive features such as actuation [6] and sensing, wide bandwidth, energy harvesting [7–12], communication [13, 14], and generate guided waves [15, 16], have been used as transducers to monitor bolted connections. The electro-mechanical impedance (EMI) method [17–22] using piezoceramic transducers has been used to monitor the loosening of the bolted connection [23–25]. Additionally, the piezoceramic transducer enabled active sensing method [26, 27] receives increasing attention in the structural health monitoring (SHM) since damages in a structure often attenuates the wave propagation [28–33]. An attenuation-based technique considering the structural damping phenomena of ultrasonic waves was used to monitor bolted looseness by Yang et al [34], and it is found that the energy dissipation, when waves propagating through the bolted joint surface, was influenced by interface integrity based on contact mechanics. Wang et al [35] investigated the signal energy received by a piezoceramic patch when ultrasonic waves propagated across the bolted joint interface under different preloads, and the response wave energy was found to be proportional to the bolt axial load, therefore, the bolt looseness could be detected. Based on the fractal contact theory and the finite element method, Huo et al [36] studied the relationship between the bolted preload and the focused signal amplitude analytically, which was obtained by using the time reversal method, then the bolted loosening could be monitored. By using the electrical resistance, Argatov and Sevostianov [37] described a method to monitor the bolted looseness, which considered the electrical constriction resistance between two rough contact interfaces.
Based on previous research results [34], it is well known that the energy dissipation across the bolted joint interface can be attributed to the damping of the structure, which is associated with the actual contact area affected by the bolt axial preload. In other words, the looseness of the bolted joints can be monitored by detecting the wave propagation and energy dissipation phenomena through the interface. Damping can be categorized into two kinds: structural damping which leads to energy dissipation at interface, and internal damping caused by material irregularities [38]. In general, the structural damping can lead to the energy consumption at contact interfaces of joints, such as fasteners and sliders [34]. Bogard et al [39] studied the damping of the bolted joint interface by experimental technique and finite element method, and the damping in tangential direction was determined to play a primary role, compared with the damping in normal direction. Therefore, this research focuses on the tangential damping.
Some scholars have conducted research to investigate the energy dissipation caused by the structural damping of the joint surface with complicated nonlinear characteristics, which can be associated with loading conditions and contact materials. Based on finite element method, Chen et al [40] studied the energy dissipation caused by the micro slip damping, and the influence of the contact pressure and shear load on the energy dissipation was investigated. Padmanabhan [41] applied the response surface methodology to predict the damping energy dissipation of the metallic joint surface under tangential loads, and developed a first-order orthogonal empirical model of energy dissipation in a vibration cycle. However, there were few published literatures about modeling the energy dissipation generated by structural damping when waves propagated across the bolted interface, which considered the imperfect interface of the bolted joints. Yang et al [34] applied the classical Hertz contact theory and the structural damping principle to attenuation-based method for monitoring the bolted loosening, but they ignored the elastic-plastic deformation process and the actual micro asperity distribution. Compared with other theories used in studying the contact surfaces, such as the classical Hertz contact theory, the fractal contact theory has some exceptional advantages, including the consideration of distribution of micro asperity of contact surface and the property of scale-independence, which is not affected by the resolution ratio of measuring instrument and the sampling length. Therefore, the fractal contact theory was used to model the energy dissipation caused by tangential damping in this paper based on consideration of the elastic-plastic deformation process, and the relationship between the bolt axial preload and the signal energy dissipation during wave propagating across the bolted joint interface was developed. The fractal contact theory [42], which is originated from the G-W contact model [43], shows that the actual contact area is significantly affected by the fractal parameters under different loads. Wang and Komvopoulos [44, 45] proposed a fractal contact model considering the elastic-plastic deformation on the basis of the previous researches, and introduced the domain extension factor to describe the microcontact size distribution. Additionally, Ervin and Sevostianov [46], Argatov and Sevostianov [47] also developed an analytical model to describe the effect of mutual positions of individual contacts on the properties of overall interfaces, and they also found that the microstructural parameters, such as the Holm's radius, were the main factors. Compared with the fractal dimension in the fractal contact theory, their method is a statistical analysis, which can also be an effective means.
By modeling the tangential damping based on the fractal contact theory, the relationship between the energy dissipation caused by the tangential damping and the bolted axial preload can be developed, when the active sensing method is applied. Then, the quantitative monitoring of the bolted looseness can be achieved in this paper, and no indirect bolt failure index, which requires a baseline measurement, is required. The energy dissipation phenomena at the imperfect interface can be obtained by inspecting wave propagation across the bolted joint surface on the basis that power transmission takes the form of waves. And the attenuated signals can be used as representation of the dissipation process, which include the time-domain wave propagation and reflection [48]. Therefore, a piezoelectric active sensing method was used to investigate the influence of the bolt pretension on the energy emitted and received by piezoelectric patches at the bolted joints. Based on the fractal contact theory, the energy dissipation modeling caused by tangential damping of the bolted structure can be developed. Then, the relationship between the bolt axial preload and the energy dissipation during the wave propagating across the interface is built, and quantitative monitoring of the bolted looseness can be achieved in this paper. Compared with the previous researches, no indirect bolt failure index is required. At last, the experiments were conducted to verify the proposed method.
2. Methodology and modeling
As mentioned above, the quantitative monitoring of the bolt looseness is achieved by developing the relationship between the energy dissipation during wave propagation and the bolt axial preload, which can be modeled analytically using the fractal contact theory and damping principles. The contact surfaces of a bolted joint, as illustrated in figure 1, are rough on the microscopic scale, and the influence of the imperfect contact surfaces on the structural damping was not considered in the previous investigations. When the wave propagates across the imperfect bolted interface, the signal energy will dissipate. Therefore, in this paper, the energy dissipation generated by the tangential damping of the bolted joints under different bolt preloads was modeled analytically based on the fractal contact theory [42], which will take the imperfect contact surfaces into account.
Figure 1. Micro contact state of bolted joint surface.
Download figure:
Standard image High-resolution imageBased on results of finite element method [49], the evolution of the elastic-plastic deformation can be divided into four stages, and the relationship between the contact load and the normal deformation δ can be described as [50],
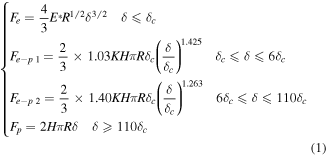
where Fe is the normal contact load in the elastic deformation stage; and
are the contact loads in the two different elastic-plastic deformation stages; Fp is the contact load in the plastic deformation stage;
is the equivalent elasticity modulus; E1 and E2 are elasticity modulus of two contact materials, respectively;
and
are Poisson's ratio of two contact materials respectively;
[51] is the hardness of the material;
is the yield strength of the material;
[52] is the coefficient of the hardness and
is the Poisson's ratio of the material; R is the radius of asperity on the rough surface, and can be expressed as
[44], where G is a scaling constant and D is a fractal dimension, which can be calculated by the power spectrum of the contact surface profile [53, 54], A' is the truncated area of a microcontact; δ is the normal deformation of asperity, which can be computed as:
[45];
[49] is the critical deformation degree of asperity.
The following equation can be obtained based on aforementioned equations of δ, δc and R,

where
By introducing the domain extension factor Wang et al [44] proposed a model to describe the microcontact size contribution, and the factor
can be obtained from the following equations,


where is the truncated area of the largest microcontact.
Then, the normal contact load of the entire bolted joint surface F can be computed by,
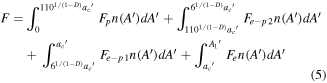
Considering the relationship between the truncated area A' and the actual contact area A proposed by Johnson [50], viz., A' = 2A, the following expression about the relationship between the axial contact load and the actual contact area of bolted joint surface can be developed by substituting equations (1), (2), and (3) into equation (5) and by using the normalization method,
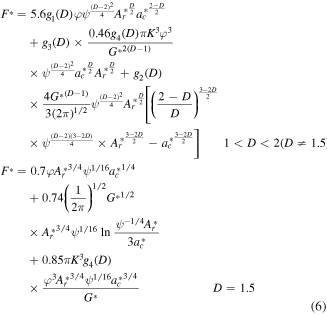
where
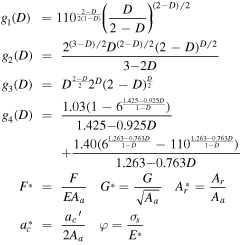
The energy dissipation caused by the tangential damping of single asperity during a vibration period under the tangential load
and the normal preload
can be expressed as [50],

where is the equivalent shear modulus;
and
are shear moduli of two contact materials, respectively; μ is the coefficient of friction; and r is the radius of the asperity's actual contact area.
In this paper, based on the hypothesis that the forces applied to the asperity are proportional to the contact area, the tangential load and the normal preload
applied to the single asperity can be calculated as,

where is the amplitude of the tangential dynamic load applied to the entire interface.
Then, with the consideration of the relationship between the truncated area A' and the actual contact area A, substituting equation (8) into equation (7) gives,

Therefore, based on the principle of the damping energy-dissipation, the energy dissipation generated by the tangential damping of the entire bolted joint under different bolt preloads can be expressed as by the normalization method,
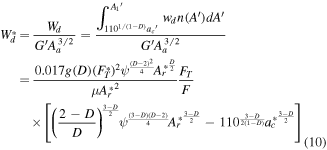
where,
The amplitude of the tangential dynamic load applied to the entire interface can be computed by the piezoelectric constitutive equation, which is shown below for a piezoceramic patch used in this paper,

where, S is the strain; T is the stress; E is the electric field; s is the compliance constant; is the piezoelectric strain coefficient; D is the electric displacement;
is the dielectric constant. And the material properties of steel and PZT patches are given in tables 1 and 2, respectively. Additionally, Roundy and Wright [55] presented a convenient method to model both the mechanical and electrical portions of piezoelectric element, and they supposed that the mechanical side of the piezoelectric element could be regarded as an uncoupled mechanical system. Therefore, the stress-strain relationship of the piezoelectric patch can be expressed as:
Then, the tangential dynamic load
can be calculated as,

Table 1. Material properties of the steel.
Material | Properties | Value |
---|---|---|
Steel | Young modulus | 209 GPa |
Shear modulus | 80 GPa | |
Poisson ratio | 0.3 | |
Density | 7860 kg m−3 | |
Yield stress | 355 MPa | |
Friction | 0.3 |
Table 2. Material properties of the piezoelectric.
Material | Properties | Value |
---|---|---|
Piezoelectric | Young modulus | 46 GPa |
Poisson ratio | 0.3 | |
Density | 7450 kg m−3 | |
Piezoelectric coefficients | ||
d31, d32 | 0.186 nC N−1 | |
d33 | 0.42 nC N−1 | |
d15 | 0.66 nC N−1 | |
Dielectric coefficients | ||
![]() |
0.1504 nF m−1 | |
![]() |
0.1301 nF m−1 |
3. Experimental setup and procedure
To verify the proposed analytical model for the energy dissipation generated by the tangential damping of the bolted joints under different bolt preloads based on the fractal contact theory, an experimental apparatus was constructed, as shown in figure 2. A torque wrench from 10 to 70 N·m was used to apply axial force on a pair of M12 bolt and nut, in order to fasten two rectangular steel plates (size: 100 mm × 60 mm × 10 mm). Two piezoelectric patches PZT 1 and PZT 2 (dimension: 10 mm × 10 mm × 1 mm), which respectively functioned as an actuator and a sensor, were bonded about 25 mm away from centerline of bolt on the two end-faces of bolted connection surface. A 10 V Gaussian pulse with a center frequency of 100 KHz was generated and converted to analog signal by using an NI multifunction DAQ device NI 6366, which was used to actuate PZT 1. An ultrasonic wave produced by PZT 1 propagated through the contact interface from the top plate to the bottom plate, and the response signal was detected by PZT 2. Then, the electrical energy stored in the piezoelectric patches can be calculated by the integral formula in the time domain [34],

where, H is the equivalent capacitance of the piezoelectric patches, which can be obtained by previous research [55]; is the voltage transmitted or received by the piezoelectric patches. Therefore, the energy dissipation during waves propagating across the bolted joint interface can be obtained by comparing the electrical energy stored in the PZT 1 and PZT 2.
Figure 2. Apparatus of the bolted joint monitoring system.
Download figure:
Standard image High-resolution imageThe roughness profiles of the two plates were measured by a phase grating interference surface roughness profiler (TALOR HOBSON, PGI 840, UK), as depicted in figure 3. The structural function of the surface profile
can be expressed as [56],

where, is the sampling length of the surface profiler; 〈〉 is the averaging over the statistical ensemble of
which can be determined by surface profiler; and C is the scaling coefficient given as [56],

Then, the fractal parameters D and G were obtained based on surface profile, and the values were respectively 1.4102 and 6.2042 × 10−13 m in this paper. Then, the variables in equations (6) and (10) can be calculated:
Figure 3. Talor Hobson surface profiler and surface profile of plates.
Download figure:
Standard image High-resolution image4. Results of the proposed method, experimental verification and discussion
Based on the modeling in section 2, the relationship between the energy dissipation generated by the tangential damping of the entire bolted joint and the bolt preloads F can be obtained, as illustrated in figure 4. The preloads were applied by the torque wrench in this paper, and the computational formula is as following,

where, d is the nominal diameter of the bolt, and T is the torque.
Figure 4. The energy dissipation under different preloads.
Download figure:
Standard image High-resolution imageIt can be observed that the energy dissipation decreases with the increase of the applied torque, and the level of reduction decreases gradually. In other words, the energy received by the piezoelectric patch increases with the increase of applied torque and a saturation value exists, which is consistent with the experimental results of Wang et al [35] and simulation results of Parvasi et al [57]. This phenomenon may be linked to the plastic deformation of interacting asperities under heavy axial load based on the hypothesis presented by Pullen et al [58], which leads to decrease of the energy dissipation caused by the structural damping. Based on experimental elicitation, Britton et al [59] and Xiao et al [60] considered that the energy dissipation could be reduced by improving the interface quality. The model proposed in this paper can be used to explain the reason: for a machined surface, the increase of roughness means smaller D and larger G, which leads to smaller actual contact area under a specific preload, viz., the energy dissipation increases based on equation (10).
By comparing the electrical energy transmitted and received by the PZT 1 and PZT 2, the energy dissipation during waves propagating across the bolted joint interface can be obtained. For instance, under 30 N·m torque level, a Gaussian pulse as depicted in figure 5(a) was actuated in PZT 1, and then the received signal as shown in figure 5(b) was accepted by PZT 2. It should be noticed that the measurement signal recorded by the PZT 2 was set in the long-term time domain as 20 ms, which was approximate to 2000 times longer than the period of the actuation wave transmitted by PZT 1. In order to verify the presented model, experiments described in section 3 under different torque levels were conducted and repeated three times, the results were depicted in figure 6. The compared results were given in table 3, which showed the error between the predicted values and the average experimental verification values. Thus, the validation of presented model in this paper can be verified.
Figure 5. (a) Transmitted signal and (b) Received signal.
Download figure:
Standard image High-resolution imageFigure 6. The Received signal energy under different torque levels.
Download figure:
Standard image High-resolution imageTable 3. Comparison of the predicted values and the experimental verification values.
Preload (N·m) | Emitted energy (J) | Received energy (J) | Measurement value (J) | Prediction value (J) | Error |
---|---|---|---|---|---|
10 | 13.1E-13 | 2.46E-13 | 10.64E-13 | 11.57E-13 | 8.74% |
20 | 13.1E-13 | 9.25E-13 | 3.85E-13 | 4.09E-13 | 6.23% |
30 | 13.1E-13 | 10.27E-13 | 2.83E-13 | 2.44E-13 | 13.78% |
40 | 13.1E-13 | 11.30E-13 | 1.80E-13 | 1.67E-13 | 7.22% |
50 | 13.1E-13 | 11.58E-13 | 1.52E-13 | 1.24E-13 | 18.42% |
60 | 13.1E-13 | 11.90E-13 | 1.20E-13 | 0.96E-13 | 20.00% |
70 | 13.1E-13 | 11.96E-13 | 1.06E-13 | 0.92E-13 | 19.30% |
Additionally, a set of experiments were conducted to explore the influence of the emitted signal's center frequency on the received energy under specific preload. The experiment results showed that the received energy decreased with the increase of the emitted signal's center frequency under 30 N·m preload, as shown in figure 7. This set of experiments demonstrated that the center frequency influenced the received energy significantly. By considering the analytical model proposed in this paper, this phenomenon can be explained. Based on equation (13), the emitted energy decreased with the decrease of the time domain, which was determined by the center frequency. The energy dissipation remained constant under specific preload, therefore, the received energy decreased with the increase of the emitted signal's center frequency.
Figure 7. Received energy under different center frequencies.
Download figure:
Standard image High-resolution image5. Conclusions
In this paper, the energy dissipation generated by the tangential damping of the bolted joints under different bolt preloads was modeled analytically based on fractal contact theory, which took the imperfect interface into account. By using active sensing method based on piezoelectric transducers, the energy dissipation during wave propagating across the bolted interface can be obtained. Then, the relationship between bolt axial preload and the energy dissipation can be established, and the method is effective to monitor and calculate bolt looseness. The phenomenon of saturation is consistent with previous research results of experiments and simulation, which can be attributed to the plastic deformation of interacting asperities under heavy load. Additionally, the center frequency of the emitted signal was demonstrated to affect the received energy significantly. Compared with previous similar studies based on experimental techniques and numerical method, the investigation presented in this paper explained the principle from the mechanism, and could achieve the quantitative monitoring of the bolted joints looseness directly, rather than an indirect bolt failure index.
More investigation should be conducted such as the equivalent contact stiffness of bolted joint interfaces considering the imperfect interface. It is well known that the equivalent contact stiffness affects the integral model frequency of the bolted joints significantly. Therefore, the model frequency change detection can be used to quantitatively monitor of the bolt loosening, by developing the relationship between the bolt preload and the equivalent stiffness analytically. Additionally, wave propagation may also be affected by the position of piezoelectric patch arrangement. A torque wrench was used to apply the preload, however, the friction variation of surface was neglect, viz., relationship between axial load and torque is not linear. Thus, a universal testing machine can be considered to use in further research.
Acknowledgments
This research was supported by the Major State Basic Development Program of China (973 Program, grant number 2015CB057704), Innovative research group project (grant number 51421064) and general project (grant numbers 51478080 and 51278084) of Natural Science Foundation of China, and the Fundamental Research Funds for the Central Universities (DUT16TD03). The authors would like to acknowledge these organizations for their financial support.