With automotive consumers increasingly seeking more seamless, connected driving experiences, the industry has increased its focus on connectivity, advanced camera systems, and the in-vehicle experience.
Continental, a leading German automotive technology company and innovator for automotive display solutions, is developing AI-powered virtual factory solutions to address these shifts and their impact on their manufacturing operations such as shorter development cycles and increased time-to-market pressures. As a pioneer of sustainable and connected technologies in automotive, their solutions are using the latest simulation and generative AI technologies to transform manufacturing operations, enhance team productivity, and accelerate innovation to meet changing consumer needs.
In addition, Continental leveraged the expertise of SoftServe, an IT consulting and digital services provider and trusted NVIDIA partner, to add generative AI functionalities to their virtual factory solutions and further enhance the efficiency of their engineering teams.
This post explains two virtual factory solutions developed on the NVIDIA Omniverse platform and Universal Scene Description (OpenUSD):
- ContiVerse: an immersive digital twin application that enables Continental’s engineers to innovate, collaborate, and drive efficiency across their global operations.
- Industrial Co-Pilot: a virtual agent that brings together generative AI and immersive 3D visualization to enable factory teams to increase productivity for maintenance.
“We chose to develop on NVIDIA Omniverse because it’s an open and easily extensible development platform,” explained Benjamin Huber, who heads advanced automation and digitalization in the UX division at Continental.
The Omniverse platform provides Continental’s developers access to the latest technologies such as RTX rendering, OpenUSD support, and capabilities for building applications and services that enable their teams to connect various systems, services, and applications into a holistic digital twin simulation. This access enables them to support their unique requirements so teams can work seamlessly across disciplines and systems.
Enhancing digital twins with ContiVerse
The ContiVerse data architecture prioritizes the flow of real-time data from processes and machinery to deliver real-time insights from factories, processes, equipment, and products. This data is aggregated into a cloud-based data lake, which serves as a foundation for simulations and AI models. The ability to access and analyze data from the cloud enables Continental teams to make informed decisions around production optimization quickly and dynamically.
Omniverse and OpenUSD enabled Continental developers to support these architectural requirements. With the flexibility of OpenUSD, they could break down data silos and facilitate multi-platform cooperation, enabling their engineers to work seamlessly across disciplines and systems.
“Any engineer, no matter what tool they’re working with, can transform their data into USD and then inter-exchange data from one discipline to another, from one tool to another,” said Huber.

The ContiVerse solution delivers significant benefits across several use cases.
Continental recently built a full-scale digital twin of one of their factories in Novi Sad, Serbia, for example, where some stations and lines are directly connected to the network. Any actions taken within the digital twin environment mirror those in the actual production line, empowering engineers to accurately assess performance and identify and resolve issues promptly.
Teams can conduct virtual Gemba walks to enhance the observation of production processes, monitor performance, and troubleshoot issues remotely through physically accurate simulations.
Using these digital twins, their teams can collaborate on the design of new lines, easily comparing different line concepts and gaining new insights into line performance, layout, shop floor space, and OEE. Engineers and simulation experts can work together to fine-tune designs, conduct detailed planning, and simulate line performance to optimize operations, all while significantly reducing engineering hours.
Creating interactive environments with Industrial Co-Pilot
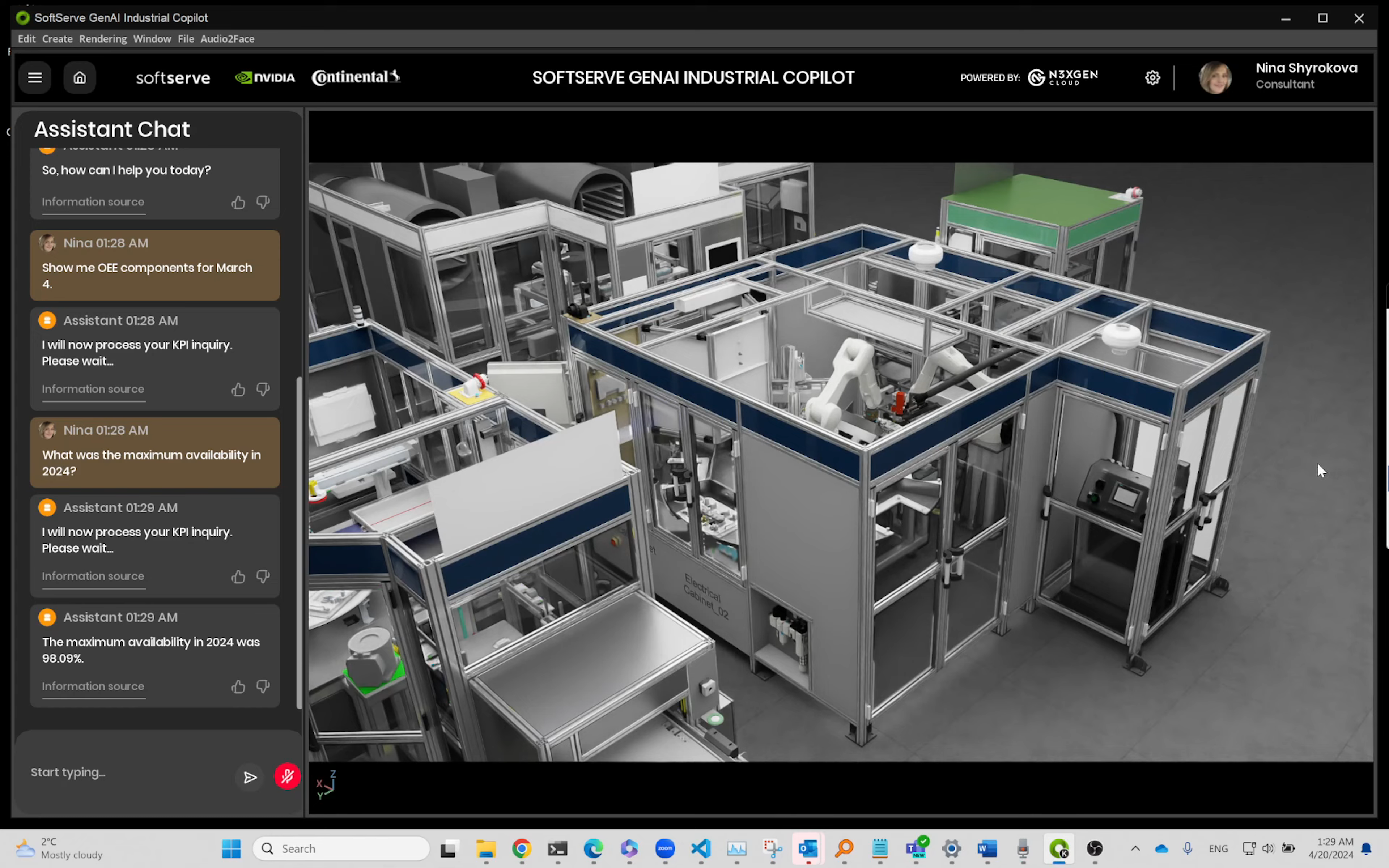
Recognizing the potential of generative AI to enhance the efficiency of their engineering teams, Continental developers also collaborated with NVIDIA partner SoftServe to develop Industrial Co-Pilot, a dynamic solution that enables Continental engineers to interact with digital twins of their production systems using natural language.
By combining AI-driven insights with immersive visualization, Industrial Co-Pilot enables Continental engineers to gain access to real-time guidance and predictive analytics, streamline maintenance procedures, and increase productivity.
Continental teams experienced significant benefits with the implementation of the solution. The use of generative AI has transformed system interactions, enabling efficient knowledge use through tasks like search, summarization, and specific task performance. Complemented by enhanced performance analysis, this provides improved data accessibility and reporting capabilities.
With Industrial Co-Pilot, engineers can connect to production lines and monitor the performance of individual stations or the entire shop floor. They can interact with the co-pilot to conduct root cause analysis and receive step-by-step work instructions and recommendations, resulting in reduced documentation processes and improved maintenance procedures. These advancements ultimately led to increased productivity and a notable 10% expected reduction in maintenance effort and downtime.
Watch the on-demand NVIDIA GTC 2024 sessions from Continental and SoftServe to learn more about their virtual factory solutions and their experience developing on NVIDIA Omniverse and OpenUSD: Transforming Factory Planning and Manufacturing Operations Within Digital Mega Plants and Getting Started With Generative AI and OpenUSD for Industrial Metaverse Applications.
Join the NVIDIA Omniverse Community live stream on May 15 to hear from Continental and SoftServe developers and learn more about their journey with digital twins and generative AI.