Microestructura
La microestructura es la configuración a muy pequeña escala de un material, definida como la estructura de la superficie preparada de un material mostrada por un microscopio óptico con un aumento de más de 25x.[1] La microestructura de un material (como metales, polímeros, cerámicas o materiales compuestos) puede influir en gran medida en propiedades físicas como la resistencia, tenacidad, ductilidad, dureza, resistencia a la corrosión, comportamiento a altas/bajas temperaturas o resistencia al desgaste. Estas propiedades a su vez gobiernan la aplicación de estos materiales en la práctica industrial.

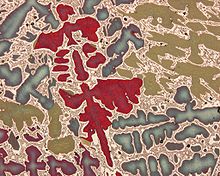
A escalas más pequeñas que las que se pueden ver con microscopio óptico, la microestructura a menudo se denomina nanoestructura, mientras que la estructura en la que se organizan los átomos individuales se conoce como estructura cristalina. La nanoestructura de las muestras biológicas se denomina ultraestructura. La influencia de una microestructura en las propiedades mecánicas y físicas de un material se rige principalmente por los diferentes defectos presentes o ausentes de la estructura. Estos defectos pueden tomar muchas formas, pero las principales son los poros. Si bien esos poros juegan un papel muy importante en la definición de las características de un material, también lo hace su composición. De hecho, para muchos materiales, pueden existir diferentes fases al mismo tiempo. Estas fases tienen diferentes propiedades y si se manejan correctamente, pueden evitar la fractura del material.
Concepto
editarEl concepto de microestructura es observable en las características macroestructurales de los objetos comunes. El acero galvanizado, como los postes de luz o las barreras de seguridad metálicas en las carreteras, exhibe un mosaico de colores no uniformes de polígonos entrelazados de diferentes tonos de gris o plata. Cada polígono es un solo cristal de zinc adherido a la superficie del acero situado por debajo. El zinc y el plomo son dos metales comunes que forman grandes cristales (granos) visibles a simple vista. Los átomos en cada grano están organizados en una de las siete disposiciones de apilamiento 3d o redes de Bravais (cúbica, tetraédrica, hexagonal, monoclínica, triclínica, romboédrica y ortorrómbica). La dirección de alineación de las matrices difiere entre los cristales adyacentes, lo que genera variaciones en la reflectividad de cada cara presentada de los granos entrelazados en la superficie galvanizada. El tamaño de grano promedio se puede controlar mediante las condiciones de procesamiento y la composición, y la mayoría de las aleaciones consisten en granos mucho más pequeños que no son visibles a simple vista. Esto permite aumentar la resistencia del material (véase endurecimiento de Hall-Petch).
Caracterización de microestructuras
editarPara cuantificar las características microestructurales, se deben caracterizar tanto las propiedades morfológicas como las materiales. El procesamiento de imágenes es una técnica muy eficaz para la determinación de características morfológicas, tales como la fracción de volumen, la morfología de inclusión,[2] el vacío,[3] y las orientaciones de los cristales. Para realizar micrografías, se usa comúnmente microscopía óptica y electrónica.
Para determinar las propiedades del material, la nanoindentación es una técnica adecuada para la determinación de propiedades de elementos cuyo tamaño es del orden de micras y submicras, para las que las pruebas convencionales no son factibles. Las pruebas mecánicas convencionales, como las pruebas de tracción o el análisis mecánico dinámico, solo pueden cuantificar propiedades macroscópicas sin ninguna indicación de propiedades microestructurales. Sin embargo, la nanoindentación se puede utilizar para la determinación de propiedades microestructurales locales de materiales homogéneos y heterogéneos. Las microestructuras[4] también se pueden caracterizar mediante modelos estadísticos de orden superior a través de los cuales se extrae de las imágenes un conjunto de propiedades estadísticas complejas. A su vez, estas propiedades se pueden usar para producir varios otros modelos estocásticos.[5][6][7]
Generación de microestructuras
editarLas microestructuras simuladas por computadora o microestructuras sintéticas, se generan para replicar las características de las microestructuras reales. Se utilizan para investigar qué característica microestructural es importante para una propiedad determinada. Para garantizar la equivalencia estadística entre las microestructuras generadas y las reales, las microestructuras se modifican después de la generación para que coincidan con las estadísticas de una microestructura real. Tal procedimiento permite la generación de un número teóricamente infinito de microestructuras simuladas por computadora que son estadísticamente iguales (tienen las mismas estadísticas) pero estocásticamente diferentes (tienen configuraciones diferentes).[3][8]
Influencia de los poros y composición
editarUn poro en una microestructura, a menos que se desee, es una desventaja para las propiedades del material. De hecho, en casi todos los materiales, un poro será el punto de partida para la aparición de una rotura, convertido en el punto de inicio de una grieta. Además, suelen ser bastante difíciles de eliminar. Las técnicas descritas más adelante involucran un proceso de alta temperatura. Sin embargo, incluso esos procesos a veces pueden hacer que el poro sea aún más grande. Los poros con un gran número de coordinación (rodeados de muchas partículas) tienden a crecer durante los procesos térmicos. Esto se debe a que la energía térmica se convierte en una fuerza impulsora para el crecimiento de las partículas que inducirán el crecimiento del poro, ya que el alto número de coordinación impide el crecimiento hacia el poro.
Para muchos materiales, se puede ver a partir de su diagrama de fase que pueden existir múltiples fases al mismo tiempo. Esas diferentes fases pueden exhibir una estructura cristalina diferente, exhibiendo así diferentes propiedades mecánicas.[9] Además, las distintas fases también exhiben una microestructura diferente (como el tamaño de grano y la orientación).[10] Este fenómeno también puede mejorar algunas propiedades mecánicas, ya que puede inducir la deflexión de las grietas, lo que retrasa la ruptura final, ya que crea una trayectoria de grietas más tortuosa en una microestructura más gruesa.[11]
Técnicas de mejora
editarEn algunos casos, el simple hecho de cambiar la forma en que se procesa el material puede influir en su microestructura. Un ejemplo es la aleación de titanio TiAl6V4.[12] Su microestructura y sus propiedades mecánicas se mejoran mediante SLM (fusión selectiva por láser), que es una técnica de impresión 3D que utiliza polvo y funde las partículas con un láser de alta potencia.[13] Otras técnicas convencionales para mejorar la microestructura son los procesos térmicos.[14]
Estos procesos se basan en el principio de que un aumento de la temperatura inducirá la reducción o aniquilación de los poros.[15] El prensado isostático en caliente (HIP) es un proceso de fabricación que se utiliza para reducir la porosidad de los metales y aumentar la densidad de muchos materiales cerámicos, lo que mejora las propiedades mecánicas y la trabajabilidad del material.[16]
El proceso HIP expone el material deseado a una presión de gas isostática, así como a alta temperatura en un recipiente sellado (a alta presión). El gas debe ser químicamente inerte para que no se produzca ninguna reacción entre él y la muestra, por lo suele utilizarse principalmente argón. La presión se logra simplemente aplicando calor al recipiente herméticamente sellado. Sin embargo, algunos sistemas también asocian el bombeo de gas al proceso para alcanzar el nivel de presión requerido. La presión aplicada sobre los materiales es igual y proviene de todas las direcciones (de ahí el término “isostático”).[17] Cuando las fundiciones se tratan con HIP, la aplicación simultánea de calor y presión elimina los vacíos internos y la microporosidad mediante una combinación de deformación plástica, fluencia y unión por difusión; este proceso mejora la resistencia a la fatiga del componente.[18]
Véase también
editarReferencias
editar- ↑ Adaptado del manual ASM Metals Handbook, Ninth Edition, v. 9, "Metallography and Microstructures", American Society for Metals, Metals Park, OH, 1985, p. 12.
- ↑ https://www.researchgate.net/publication/279771139_Uncorrelated_volume_element_for_stochastic_modeling_of_microstructures_based_on_local_fiber_volume_fraction_variation
- ↑ a b c https://www.researchgate.net/publication/305803249_Characterization_synthetic_generation_and_statistical_equivalence_of_composite_microstructures
- ↑ https://www.researchgate.net/publication/292208855_Length-scale_dependence_of_variability_in_epoxy_modulus_extracted_from_composite_prepreg
- ↑ Tahmasebi, Pejman (20 de febrero de 2018). «Accurate modeling and evaluation of microstructures in complex materials». Physical Review E 97 (2): 023307. Bibcode:2018PhRvE..97b3307T. PMID 29548238. doi:10.1103/PhysRevE.97.023307.
- ↑ Tahmasebi, Pejman (2018). «Nanoscale and multiresolution models for shale samples». Fuel (en inglés) 217: 218-225. doi:10.1016/j.fuel.2017.12.107.
- ↑ Tahmasebi, Pejman; Sahimi, Muhammad (29 de junio de 2018). «A stochastic multiscale algorithm for modeling complex granular materials». Granular Matter 20 (3). ISSN 1434-5021. S2CID 85549903. doi:10.1007/s10035-018-0816-z.
- ↑ Tahmasebi, Pejman (20 de febrero de 2018). «Accurate modeling and evaluation of microstructures in complex materials». Physical Review E 97 (2): 023307. Bibcode:2018PhRvE..97b3307T. ISSN 2470-0045. PMID 29548238. doi:10.1103/physreve.97.023307.
- ↑ Oberwinkler, B., Modeling the fatigue crack growth behavior of Ti-6Al-4V by considering grain size and stress ratio. Materials Science and Engineering: A 2011, 528 (18), 5983-5992.
- ↑ Sieniawski, J.; Ziaja, W.; Kubiak, K.; Motyka, M., Microstructure and mechanical properties of high strength two-phase titanium alloys. Titanium Alloys-Advances in Properties Control 2013, 69-80.
- ↑ Nalla, R.; Boyce, B.; Campbell, J.; Peters, J.; Ritchie, R., Influence of microstructure on high-cycle fatigue of Ti-6Al-4V: bimodal vs. lamellar structures. Metallurgical and Materials Transactions A 2002, 33 (13), 899-918.
- ↑ Henriques, V. A. R.; Campos, P. P. d.; Cairo, C. A. A.; Bressiani, J. C., Production of titanium alloys for advanced aerospace systems by powder metallurgy. Materials Research 2005, 8 (4), 443-446.
- ↑ Kruth, J.-P.; Mercelis, P.; Van Vaerenbergh, J.; Froyen, L.; Rombouts, M., Binding mechanisms in selective laser sintering and selective laser melting. Rapid prototyping journal 2005, 11 (1), 26-36.
- ↑ Murr, L.; Quinones, S.; Gaytan, S.; Lopez, M.; Rodela, A.; Martinez, E.; Hernandez, D.; Martinez, E.; Medina, F.; Wicker, R., Microstructure and mechanical behavior of Ti–6Al–4V produced by rapid-layer manufacturing, for biomedical applications. Journal of the mechanical behavior of biomedical materials 2009, 2 (1), 20-32.
- ↑ Kasperovich, G.; Hausmann, J., Improvement of fatigue resistance and ductility of TiAl6V4 processed by selective laser melting. Journal of Materials Processing Technology 2015, 220, 202-214.
- ↑ Lin, C. Y.; Wirtz, T.; LaMarca, F.; Hollister, S. J., Structural and mechanical evaluations of a topology optimized titanium interbody fusion cage fabricated by selective laser melting process. Journal of Biomedical Materials Research Part A 2007, 83 (2), 272-279.
- ↑ Leuders, S.; Thöne, M.; Riemer, A.; Niendorf, T.; Tröster, T.; Richard, H.; Maier, H., On the mechanical behaviour of titanium alloy TiAl6V4 manufactured by selective laser melting: Fatigue resistance and crack growth performance. International Journal of Fatigue 2013, 48, 300-307.
- ↑ Larker, H. T.; Larker, R., Hot isostatic pressing. Materials Science and Technology 1991.
Enlaces externos
editar- Wikimedia Commons alberga una categoría multimedia sobre Microestructura.