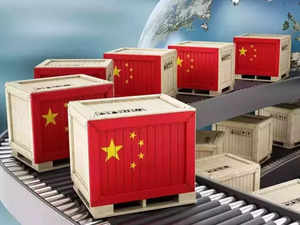
At the recent Computex trade show in Taipei, exhibitors ranging from power-tool suppliers and auto-electronics vendors to server and laptop makers, told me almost identical stories. They’re moving operations out of China and into Southeast Asia, largely at the behest of major foreign clients. Thailand, Vietnam and Taiwan are the focus of new investments. But they also warn that once the initial migration phases are complete, subsequent decoupling will be much harder.
Assembly of final products is the easiest because it’s labour intensive, and the equipment used is simple. Then comes semi-completed manufacturing, such as product housings and casings. Such transfer is quick and cheap, and well underway. Mexico is now the largest source of imports to the US, while factories in India, Vietnam and Thailand are taking share from Chinese counterparts.
If we look only at final assembly, it’s easy to conclude that full supply chain migration is achievable.
But most of the hard work and value-add happens many steps before final production, using specialized, expensive equipment operated by well-trained technicians. Plastic and metal molding is one example. This phase relies heavily on networks of suppliers close at hand. Over the past two decades China has built up considerable capacity and expertise in the crucial and hidden ingredient of all industries: chemicals. Hundreds of factories dotted around the country specialize in semi-processed compounds known as intermediates.
China accounts for more than 40% of global chemical production, according to one estimate. It has a 55% share of acetic acid capacity, a relatively banal substance that’s the core component of vinegar, but also used to make glue, textiles, dyes, rubber and plastics, and agricultural products. The country also holds around 45% of the world’s titanium oxide manufacturing capabilities, an ingredient in paints, paper and various coatings.
Because this concentration of chemical factories creates a cluster effect, makers of related products such as plastics and metals that go into toys, packaging, electronics, automobiles and machines risk losing speed and efficiency if they start moving too much of their operations abroad. Taiwanese and foreign exhibitors at Computex explained that while they’re already expanding in Southeast Asia, their own suppliers — chemicals, plastics and metals makers — aren’t in much of a hurry. That creates a natural limit to how much of a supply chain can be exfiltrated from China, even if sweeteners like free land, tax breaks and cheap utilities are on offer.
The current global economic environment works against migration, standing in contrast to the increasingly tense geopolitical situation that adds urgency to decoupling. First, a recent downturn in the materials sector, where China is a leader, means suppliers of intermediate chemicals aren’t in the financial position to dedicate new capital expenditure to foreign plants.
In addition, recent easing of supply chain constraints and higher availability of transport capacity softens the urgency to move all parts of the manufacturing equation to alternative hubs. There’s no need to spend millions of dollars on a new plant if there are plenty of ships on hand to move half-finished goods in bulk across the South China Sea to assembly sites in Southeast Asia.
It will take massive incentives and a willingness from clients to accept higher prices before more manufacturers can afford to make the move away from the hubs they built in China over the past few decades. The alternative catalyst, an unthinkable shock like war or political upheaval, would also provide the impetus. But by the time that happens, it’ll be too late.
Complete, end-to-end, migration of supply chains is difficult and expensive. But if it is to be undertaken, the move is best done now, in a time of peace and tranquility, than during a period of urgency.
(Catch all the Business News, Breaking News, Budget 2024 Events and Latest News Updates on The Economic Times.)
Subscribe to The Economic Times Prime and read the ET ePaper online.
(Catch all the Business News, Breaking News, Budget 2024 Events and Latest News Updates on The Economic Times.)
Subscribe to The Economic Times Prime and read the ET ePaper online.